Comprehending What is Porosity in Welding: Reasons and Solutions
Wiki Article
Comprehending Porosity in Welding: Discovering Causes, Effects, and Avoidance Strategies
As professionals in the welding sector are well conscious, comprehending the causes, impacts, and avoidance methods connected to porosity is essential for accomplishing durable and dependable welds. By diving right into the root causes of porosity, analyzing its detrimental results on weld high quality, and exploring reliable prevention techniques, welders can boost their knowledge and skills to create top quality welds regularly.Typical Reasons For Porosity
Contamination, in the type of dirt, grease, or corrosion on the welding surface, creates gas pockets when warmed, leading to porosity in the weld. Inappropriate protecting occurs when the securing gas, typically utilized in procedures like MIG and TIG welding, is incapable to totally shield the molten weld pool from reacting with the bordering air, resulting in gas entrapment and subsequent porosity. Furthermore, insufficient gas protection, typically due to incorrect flow prices or nozzle positioning, can leave parts of the weld unguarded, permitting porosity to develop.Effects on Weld Top Quality
The visibility of porosity in a weld can significantly compromise the total high quality and stability of the bonded joint. Porosity within a weld produces voids or cavities that deteriorate the structure, making it more susceptible to splitting, deterioration, and mechanical failing.Additionally, porosity can hinder the effectiveness of non-destructive testing (NDT) methods, making it testing to discover other issues or gaps within the weld. This can cause substantial security worries, specifically in critical applications where the structural integrity of the welded elements is paramount.
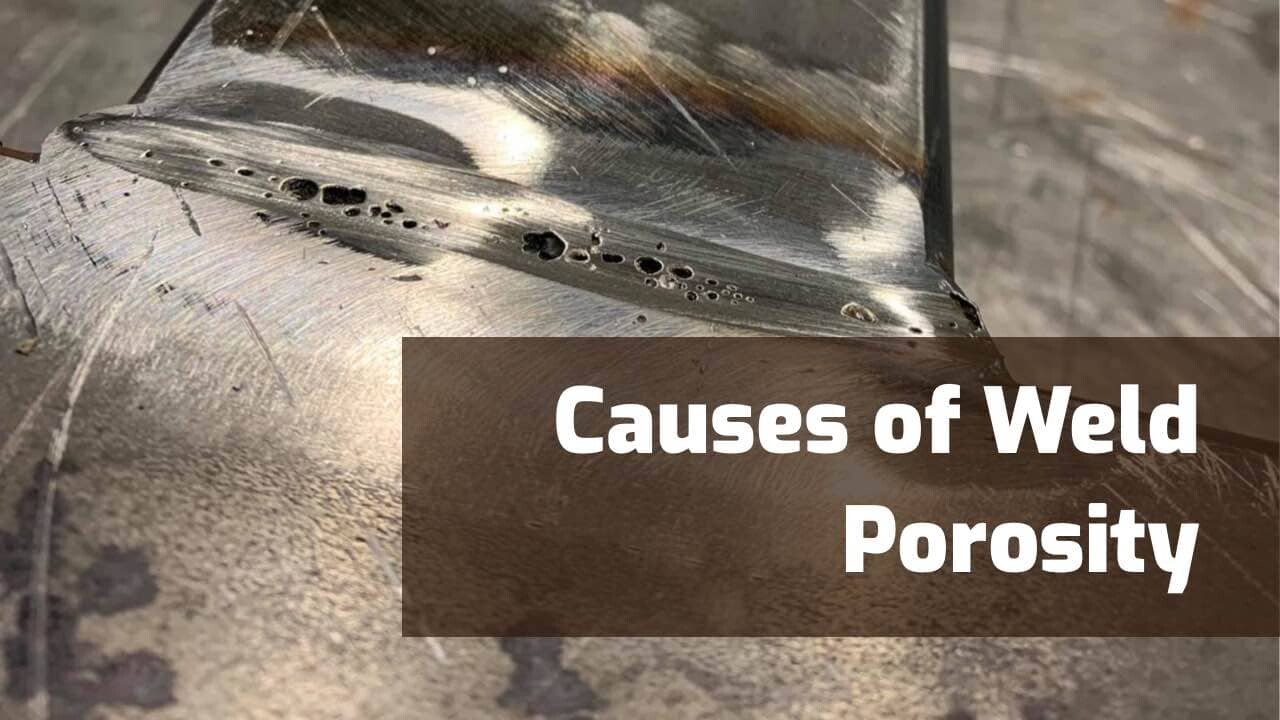
Prevention Techniques Introduction
Given the harmful influence of porosity on weld quality, efficient avoidance strategies are important to keeping the architectural honesty of welded joints. In addition, selecting the appropriate welding specifications, such as voltage, existing, and take a trip rate, can assist reduce the threat of porosity formation. By incorporating these avoidance techniques into welding techniques, the incident of porosity can be significantly reduced, leading to more powerful and extra reliable bonded joints.Relevance of Proper Protecting
Proper shielding in welding plays a vital function in stopping climatic contamination and guaranteeing the honesty of bonded joints. Shielding gases, such as argon, helium, or a combination of both, are frequently made use of to secure the weld swimming pool go from responding with elements airborne like oxygen and nitrogen. When these responsive components enter contact with the warm weld swimming pool, they can cause porosity, causing weak welds with lowered mechanical buildings.
Poor protecting can cause different issues like porosity, spatter, and oxidation, endangering the structural honesty of the welded joint. Therefore, adhering to appropriate shielding techniques is vital to generate high-quality welds with marginal issues and make sure the durability and dependability of the welded parts (What is Porosity).
Monitoring and Control Techniques
Just how can welders efficiently keep an eye on and regulate the welding process to make certain optimal results and stop problems like porosity? By constantly keeping track of these variables, welders can determine deviations from the ideal problems and make instant changes to stop porosity formation.
Furthermore, carrying out appropriate training view publisher site programs for welders is important for keeping track of and managing the welding procedure effectively. What is Porosity. Educating welders on the relevance of keeping consistent parameters, such as correct gas protecting and take a trip rate, can aid stop porosity concerns. Normal analyses and certifications can likewise make certain that welders excel in monitoring and controlling welding processes
Moreover, the usage of automated welding systems can improve monitoring and control capacities. These systems can exactly regulate their explanation welding parameters, lowering the probability of human error and making sure consistent weld top quality. By incorporating advanced surveillance innovations, training programs, and automated systems, welders can efficiently check and control the welding process to minimize porosity issues and accomplish high-quality welds.
Conclusion
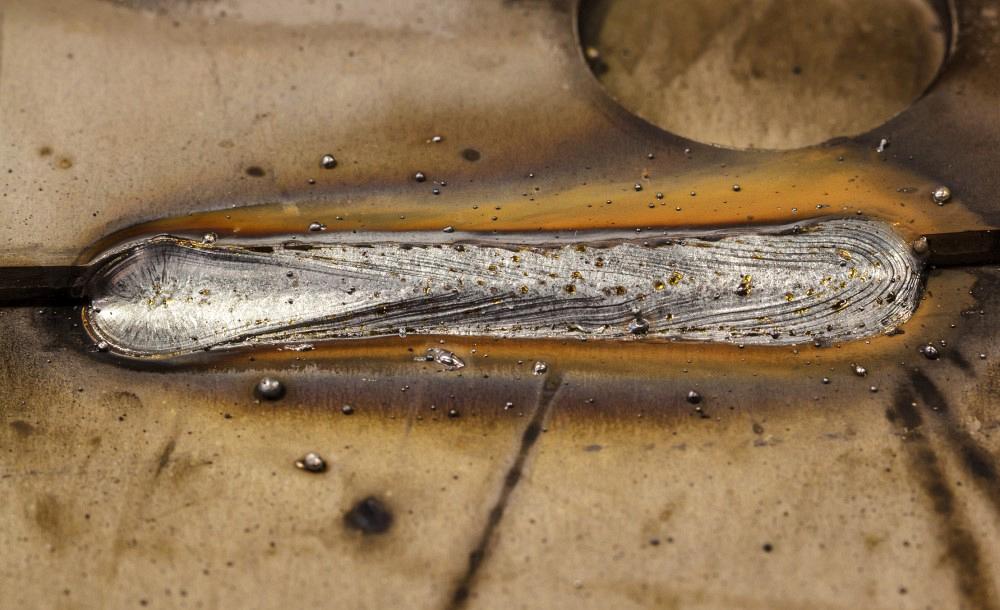
Report this wiki page